Cavity/Core Material | P20,718,2738,H13,DIN1,2311 or as customer quested |
Product Raw Material | PP |
Cacity | Multi Cavity |
Cycle Time | 20S |
Runner System | Hot runner,Cold runner |
Finish | Good Polishing |
Mold Guarantee | 500,000 Shots |
Mould Standard | HASCO,DME,or by requested etc. |
Software | CAD,Pro-E,UG,Solidwork |
Tolerance | ± 0.02mm |
Main Technique | Milling, Grinding, CNC , Engraving ,EDM, Wire-cutting etc. |
Packing | Wooden Canse |
Payment Terms | 50% deposit by T/T,balance against B/L copy |
Port | Ningbo Port |
Lead Time | 40-45 days |
1.Quote |
According Sample or 2D/3D drawing or Picture with detailed information , If the part some design is not good , we will give suggestion and solutions to customer |
          ↓ | |
2.Discussion |
Mold material, cavity number, price, runner, payment, etc. |
          ↓ | |
3.Approved |
Order confirmed |
          ↓ | |
4. Advance |
Pay 50% by T/T |
          ↓ | |
5.Product Design Checking. |
We will send 2D and 3D part drawing and PPT file for customer check |
          ↓                    | |
5.Mould Design |
According the Approved Part drawing , we will make the mold design and send to customer confirm |
          ↓ | |
6.Mold Steel Material and Component Prepare |
After drawing confirmed , we will start to prepare the steel material and standard components |
          ↓ | |
7.Mold Processing |
Send detailed reports with pictures to customer each week |
          ↓ | |
8.Mold Testing |
Send Test samples with report to customer |
          ↓ | |
9. Mold Modification |
According to customer's feedback |
          ↓ |
 |
10.Balance settlement |
50% by T/T after the customer approved the test sample and mould quality. |
          ↓ |
 |
11.Packing and Delivery |
Each Mold will be packing with some damageable spare parts , and send detailed pictures to customer |
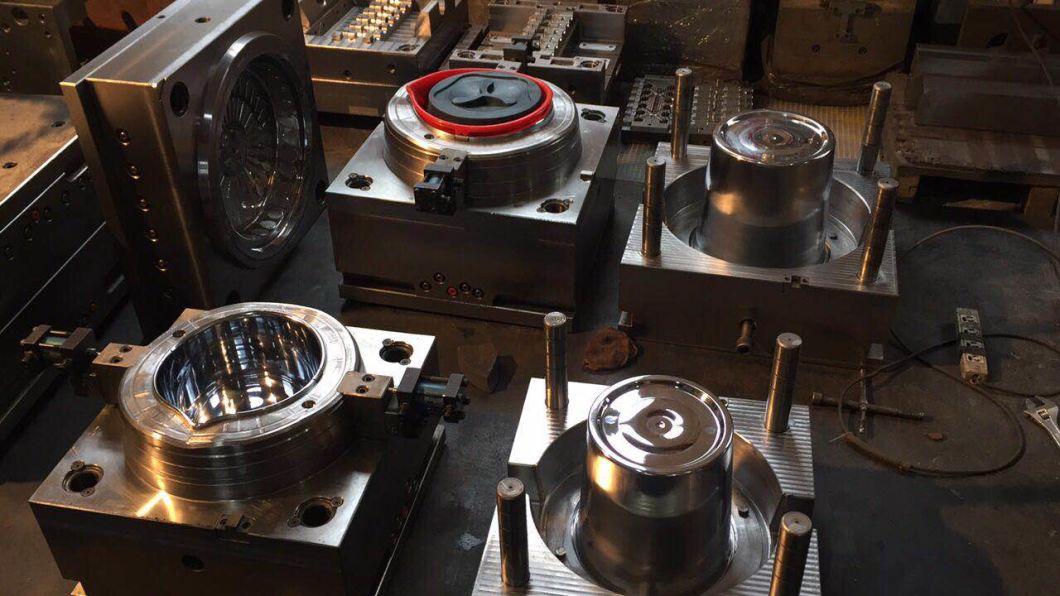
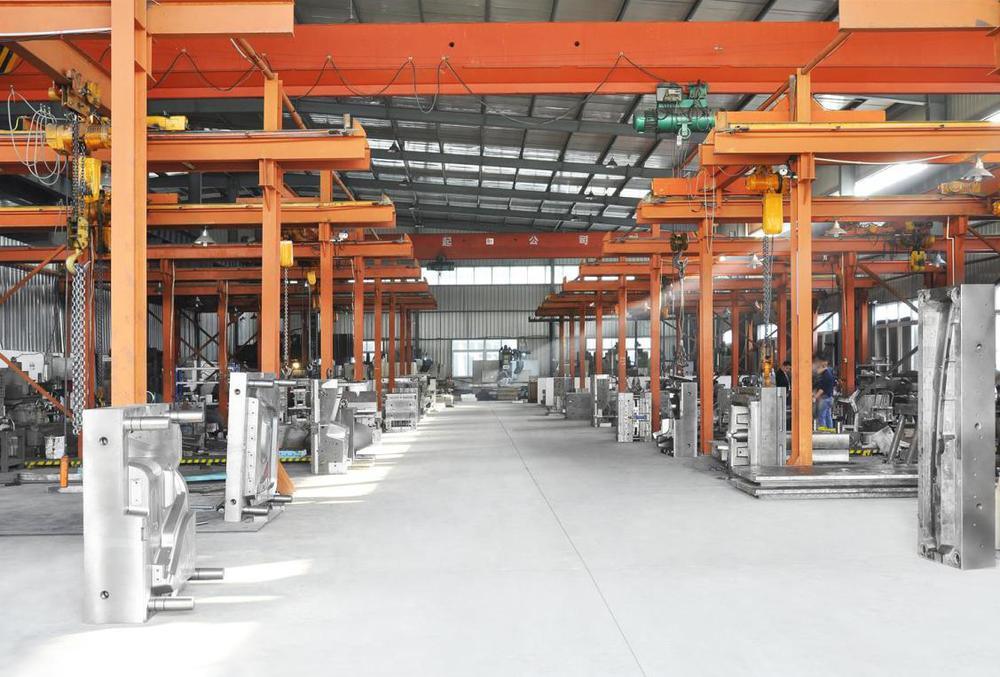
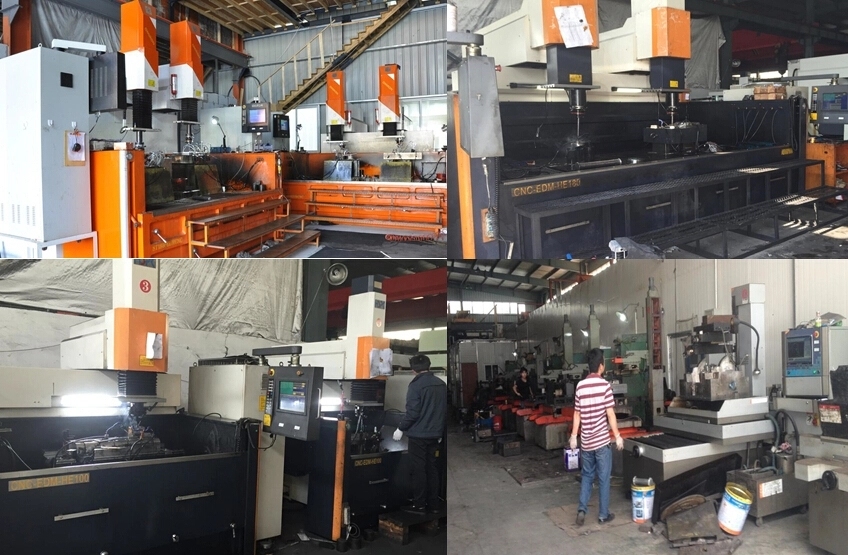
Â
Q/C Inspect Moulds:
1.Mould Material Q/C
- Mould Steel Checking(Hardness, Crack ,Blow hole material defects )
- Mould Standard Spare Parts Checking(hardness, size, flaw checking)
2. Mould Machining Process Q/C
- Design checking (Part design, mould design,Including 2D drawing and 3D drawing)Â
- Each part of mould's size checking after machining according to 2D drawing
- Mold Test (check mould running conditions and T1 samples)
3.Make sure to follow and checking each points of customer's request before shipment
Compared to metal materials, plastics offer many advantages in cost, design, processing and performance. The inherent design freedom of plastic molding ensures more efficient gear manufacturing. Internal gears, gear sets, worm gears, etc. can be molded from plastic. Plastic gears have a wider application area than metal gears, so they push gears toward higher loads and greater power transmission.
Plastic Gear Mold,Plastic Injection Mould,High Accuracy Plastic Injection Moulds,Plastic Small Gear Mould
Dongguan Kaisijin Intelligent Technology Co., Ltd , https://www.oemsmartlock.com