Certificate: ISO9001: 2000 & 14001: 2004
Design service: Acoording to clients' requirements.
Material ABS. PP. PVC. PE. PC. HIPS. POM. PA6. PA66, etc
Processing: Mould design, Mold flow, CNC process, EDM process, mold making, testing, production, packing
Machining CNC Drilling, CNC Turning, Milling, Grinding, Tapping, etc.
Mold life time: 300000 shots
Application: Auto part. Electronic. Construction fitting. Machine components. Lighting
Advantages
1. Experienced and professioanl staff;
2. Complete solution from Design- Sample-Production- shipping to make you more competitive;
3. Strickt management and excellent QC system for the high quanlity. (5S+PDCA);
4. Advanced equipment and precise measuring machine.
5. High quanlity but competitve pricing.
6. In- house Powder coating facility and Full Assembly capacity;
7. We are specilalized in Precision Die-casting, Plastic injection and molding.
Delivery 15-30 days after order confirmation.
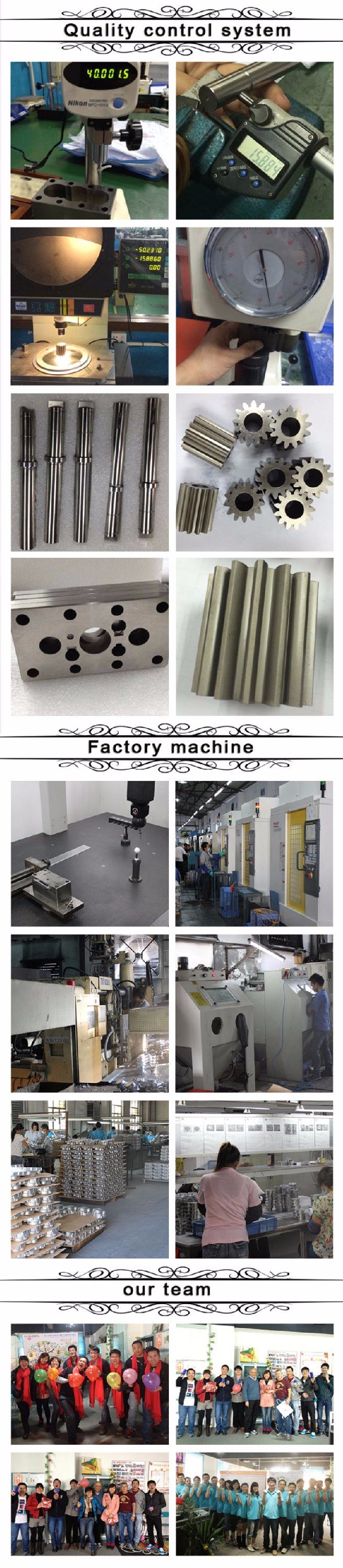
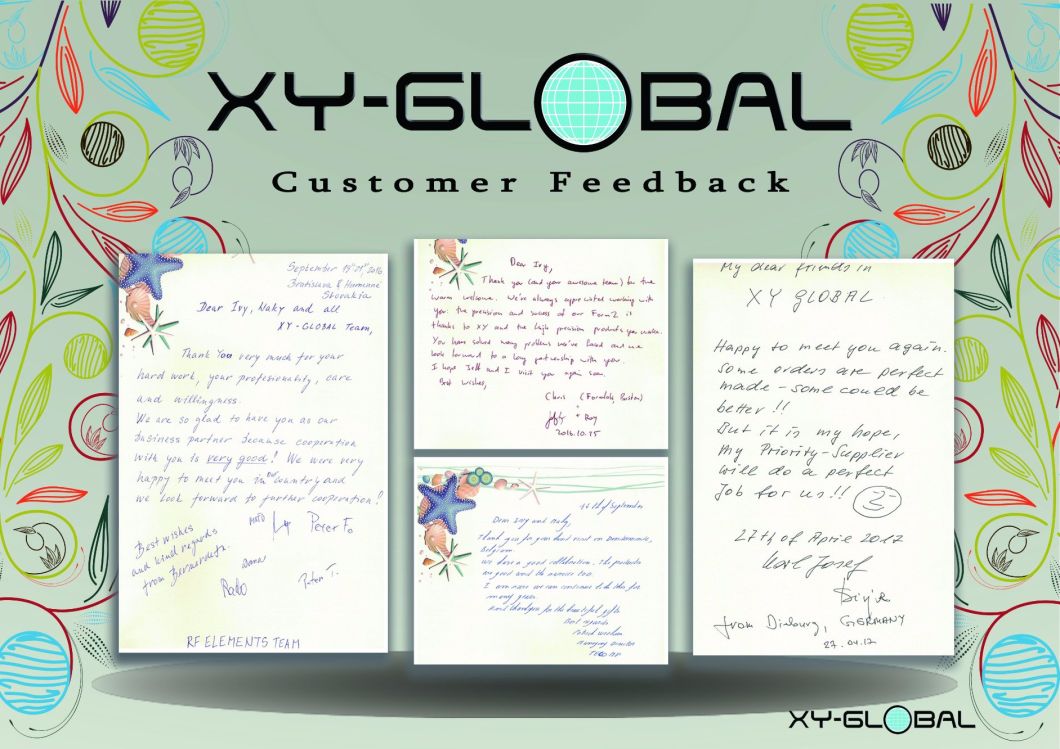
Â
"Gravity Die Casting. A permanent mould casting process, where the molten metal is poured from a vessle of ladle into the mould, and cavity fills with no force other than gravity, in a similar manner to the production of sand castings, although filling cn be controlled by tilting the die."
Gravity Die Casting
Sometimes referred to as Permanent Mould, GDC is a repeatable casting process used for non-ferrous alloy parts, typically aluminium, Zinc and Copper Base alloys.
The process differs from HPDC in that Gravity- rather than high pressure- is used to fill the mould with the liquid alloy.
GDC is suited to medium to high volumes products and typically parts are of a heavier sections than HPDC, but thinner sections than sand casting.
There are three key stages in the process.
- The heated mould [Die or Tool] is coated with a die release agent. The release agent spray also has a secondary function in that it aids cooling of the mould face after the previous part has been removed from the die.
- Molten metal is poured into channels in the tool to allow the material to fill all the extremities of the mould cavity. The metal is either hand poured using steel ladles or dosed using mechanical methods. Typically, there is a mould [down sprue" that allows the alloy to enter the mould cavity from the lower part of the die, reducing the formation of turbulence and subsequent porosity and inclusions in the finished part.
- Once the part has cooled sufficiently, the die is opened, either manually or utilising mechanical methods.
Advantages
- Good dimensional accuracy
- Smoother cast surface finish than sand casting
- Improved mechanical properties compared to sand casting
- Thinner walls can be cast compared to sand casting
- Reverse draft internal pockets and forms can be cast in using preformed sand core inserts
- Steel pins and inserts can be cast in to the part
- Faster production times compared to other processes.
- Once the tolling is proven, the product quality is very repeatable.
- Outsourced Tooling setup costs can be lower than sand casting.
Gravity Casting Parts,Aluminum Alloy Gravity Casting Parts,Aluminum Gravity Die Casting Parts,Gravity Casting Aluminum Parts
HSI INDUSTRIEL LTD , https://www.hsiindustriel.com