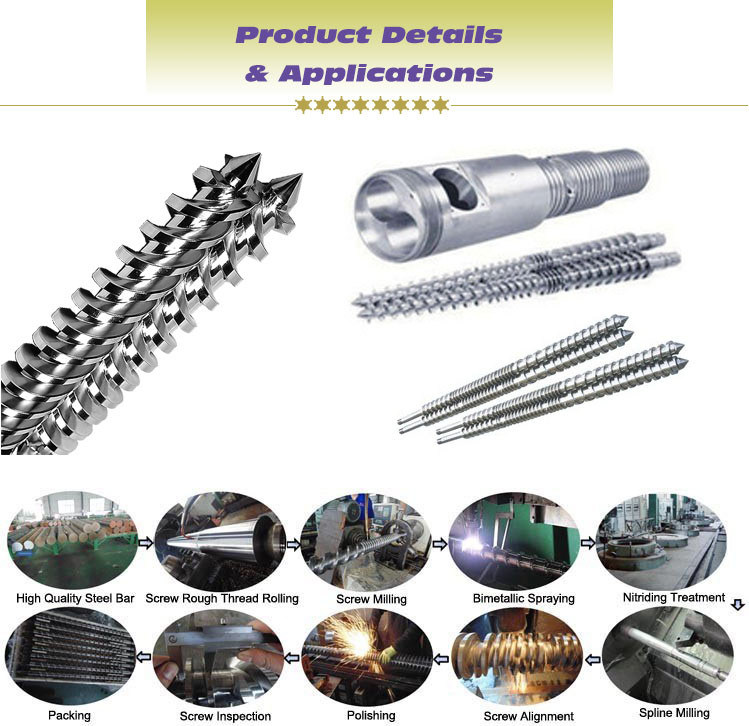
Technical Information for Parallel Twin Screw Barrel | |||
Main Base materials | 1.38CrMoAlA (SACM645) | Main Alloy Materials | 1. Ni-based alloy/Deloro alloy |
2. SKD-61 (Special Tool Steel) | 2. Tungsten carbide/Wolfram carbide | ||
3. 42CrMo (Ultrahigh StrengthSteel) | 3. NiCo-based alloy | ||
4. DC53 (Cold WorkDie Steel) | 4. Fe-based alloy | ||
5. W6Mo5Cr4V2 (High-SpeedToolSteel) | 5. Co-based alloy | ||
Processing Technics | 1. Heat treatment | Technical parameters | Nitriding layer depth:0.5-0.8mm |
2. Quenching | Nitrided hardness:900-1000HV | ||
3. Nitriding treatment | Bimetallic layer depth:3 mm | ||
4. Bimetallic alloy welding for screw | Bimetallic hardness:57~69HRC | ||
5. Bimetallic alloy centrifugal casting for barrel | Hard-chrome plating hardness after nitriding:≥950HV | ||
6. Hard-chrome electroplating | Chrome-plating layer depth:0.03-0.09mm | ||
Linearity of screw:0.015mm | Surface roughness:Ra 0.4 |
The most common types of conical twin screw barrel extruder | |||
types of screw (d/D) | length of work(mm) | quantity ofextruder(kg/h) | speed of screw rotate(rpm) |
Φ35/77 | 810 | 40-70 | 5~50 |
Φ45/99 | 990 | 50-80 | 5~45 |
Φ51/105 | 1070 | 100-150 | 4~45 |
Φ51/105 | 1220 | 100-150 | 4~45 |
Φ55/110 | 1220 | 120-180 | 4~40 |
Φ60/125 | 1320 | 150-200 | 4~40 |
Φ65/120 | 1440 | 200-250 | 4~40 |
Φ65/132 | 1440 | 200-250 | 4~40 |
Φ70/140 | 1460 | 220-300 | 4~40 |
Φ75/150 | 1480 | 250-320 | 4~35 |
Φ80/143 | 1660 | 300-360 | 4~35 |
Φ80/156 | 1800 | 300-360 | 4~35 |
Φ90/184 | 2000 | 400-500 | 3~35 |
The most common types of parallel twin screw barrel extruder | ||||||
D35/5 | D45/2 | D50/2 | D60/2 | D65/2 | D70/2Â Â | D72/2 |
D75/2 | D80/2 | D85/2 | D90/2 | D93/2 | D100/2 | D105/2 |
D110/2 | D115/2 | D120/2 | D125/2 | D130/2 | D140/2 | D150/2 |
D160/2 | D170/2 | D180/2 | D190/2 | D200/2 | D200/2 | D250/2 |
Screw types:
Gradual change, chop, barrier, distributary, separate, air exhausting, pin, mixing and etc.
For good plasticizing effect, we have different design of screw barrel to meet customer's demand.
Specification :
Dia 20mm-250mm; L/D=15-45
Scope of Application:
1. Generally plastic material
2. Pipe/ Profile/ Sheet/Pelletizing
3. WPC, ABS, TPR, TPU, PMMA, C-PVC, UPVC, RPVC, PET, EVA, PU,PE etc
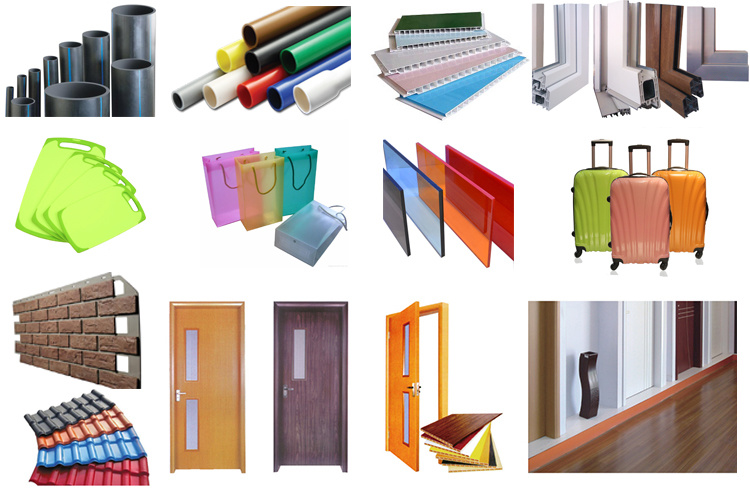
Treatment:
Nitrized, Chrome coating, Quenching, Bimetallic
We are foucs on each process to make sure each screw barrel is qualified according to technical requirement.Â
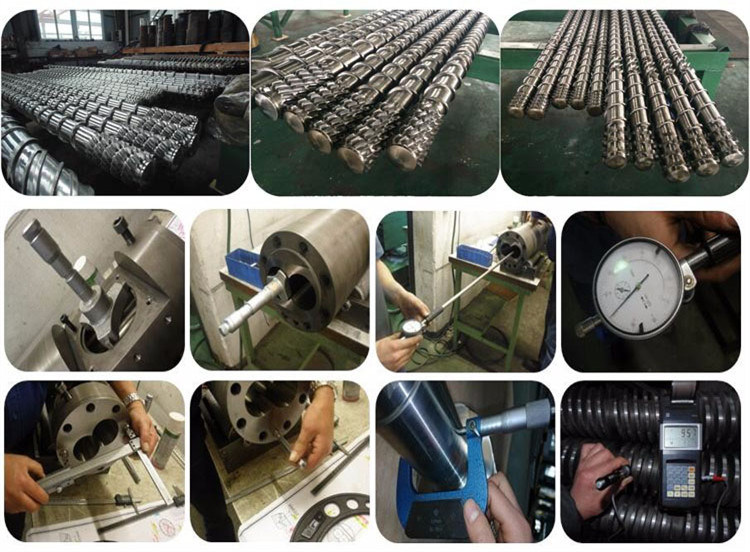
Packaging Details:
1. Be brushed anti-corrosive oil on extruder machine single screw.Â
2. Packed with film.Â
3. Packed in the AA wooden.
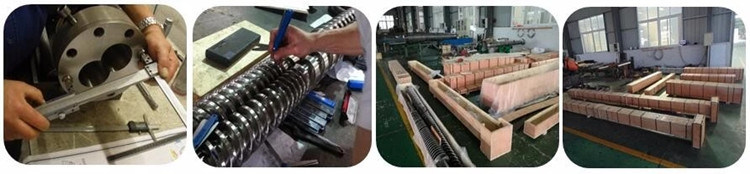
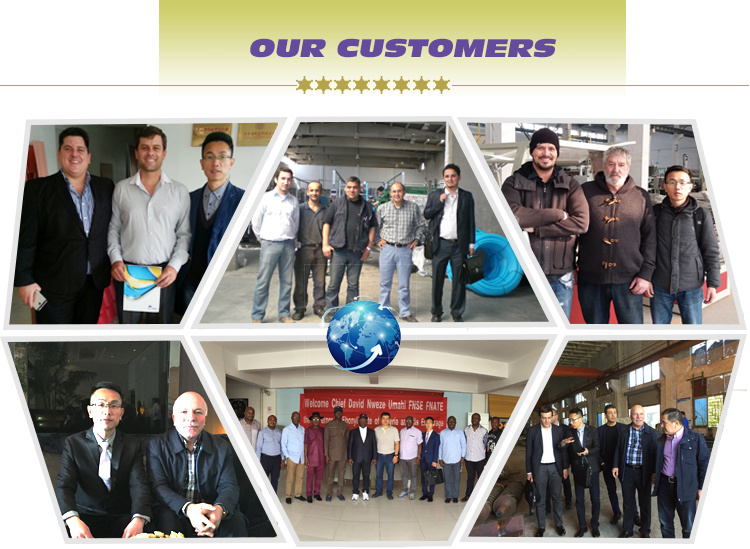
Please provide samples or requirements about dimensions and tolerances of , semi-finished and finished products, the equipment, the monthlly comsumption quantity, the current screw and barrel you are using, HRC and so on.
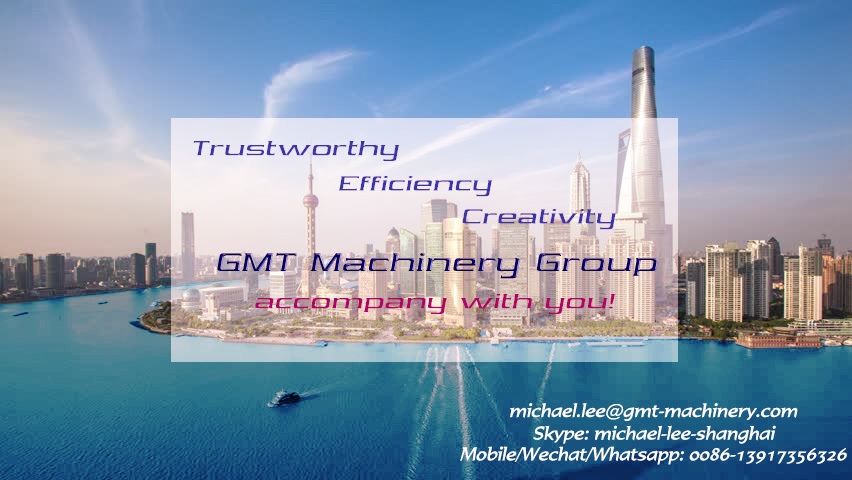
For more information, please kindly contact as below:
Mobile: 0086-13917356326
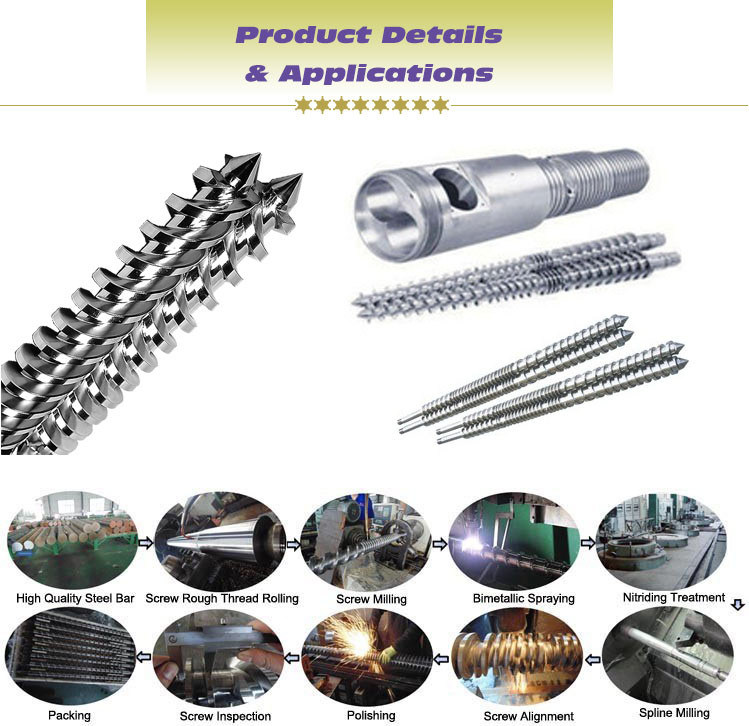
Technical Information for Parallel Twin Screw Barrel | |||
Main Base materials | 1.38CrMoAlA (SACM645) | Main Alloy Materials | 1. Ni-based alloy/Deloro alloy |
2. SKD-61 (Special Tool Steel) | 2. Tungsten carbide/Wolfram carbide | ||
3. 42CrMo (Ultrahigh StrengthSteel) | 3. NiCo-based alloy | ||
4. DC53 (Cold WorkDie Steel) | 4. Fe-based alloy | ||
5. W6Mo5Cr4V2 (High-SpeedToolSteel) | 5. Co-based alloy | ||
Processing Technics | 1. Heat treatment | Technical parameters | Nitriding layer depth:0.5-0.8mm |
2. Quenching | Nitrided hardness:900-1000HV | ||
3. Nitriding treatment | Bimetallic layer depth:3 mm | ||
4. Bimetallic alloy welding for screw | Bimetallic hardness:57~69HRC | ||
5. Bimetallic alloy centrifugal casting for barrel | Hard-chrome plating hardness after nitriding:≥950HV | ||
6. Hard-chrome electroplating | Chrome-plating layer depth:0.03-0.09mm | ||
Linearity of screw:0.015mm | Surface roughness:Ra 0.4 |
The most common types of conical twin screw barrel extruder | |||
types of screw (d/D) | length of work(mm) | quantity ofextruder(kg/h) | speed of screw rotate(rpm) |
Φ35/77 | 810 | 40-70 | 5~50 |
Φ45/99 | 990 | 50-80 | 5~45 |
Φ51/105 | 1070 | 100-150 | 4~45 |
Φ51/105 | 1220 | 100-150 | 4~45 |
Φ55/110 | 1220 | 120-180 | 4~40 |
Φ60/125 | 1320 | 150-200 | 4~40 |
Φ65/120 | 1440 | 200-250 | 4~40 |
Φ65/132 | 1440 | 200-250 | 4~40 |
Φ70/140 | 1460 | 220-300 | 4~40 |
Φ75/150 | 1480 | 250-320 | 4~35 |
Φ80/143 | 1660 | 300-360 | 4~35 |
Φ80/156 | 1800 | 300-360 | 4~35 |
Φ90/184 | 2000 | 400-500 | 3~35 |
The most common types of parallel twin screw barrel extruder | ||||||
D35/5 | D45/2 | D50/2 | D60/2 | D65/2 | D70/2Â Â | D72/2 |
D75/2 | D80/2 | D85/2 | D90/2 | D93/2 | D100/2 | D105/2 |
D110/2 | D115/2 | D120/2 | D125/2 | D130/2 | D140/2 | D150/2 |
D160/2 | D170/2 | D180/2 | D190/2 | D200/2 | D200/2 | D250/2 |
Screw types:
Gradual change, chop, barrier, distributary, separate, air exhausting, pin, mixing and etc.
For good plasticizing effect, we have different design of screw barrel to meet customer's demand.
Specification :
Dia 20mm-250mm; L/D=15-45
Scope of Application:
1. Generally plastic material
2. Pipe/ Profile/ Sheet/Pelletizing
3. WPC, ABS, TPR, TPU, PMMA, C-PVC, UPVC, RPVC, PET, EVA, PU,PE etc
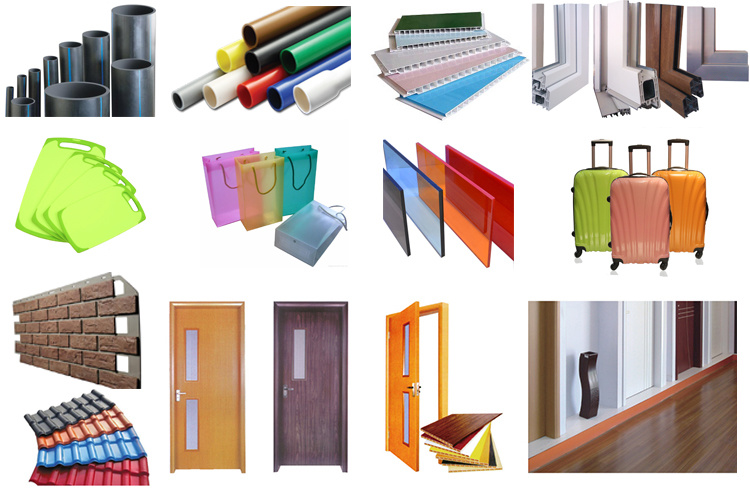
Treatment:
Nitrized, Chrome coating, Quenching, Bimetallic
We are foucs on each process to make sure each screw barrel is qualified according to technical requirement.Â
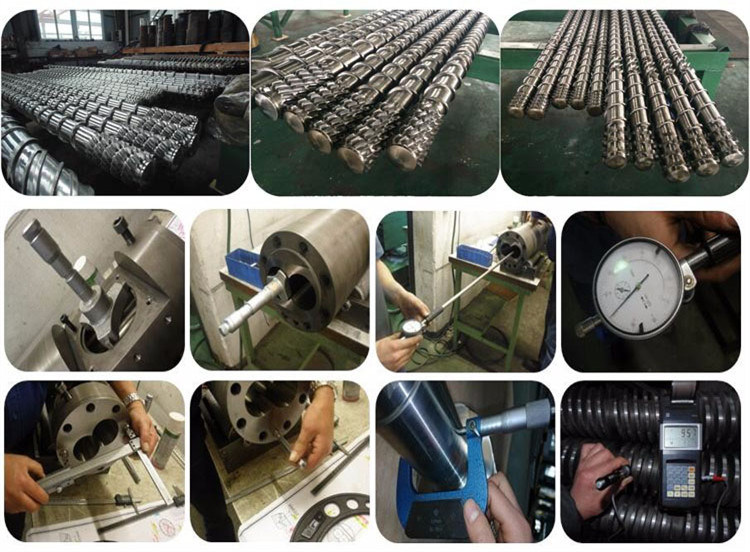
Packaging Details:
1. Be brushed anti-corrosive oil on extruder machine single screw.Â
2. Packed with film.Â
3. Packed in the AA wooden.
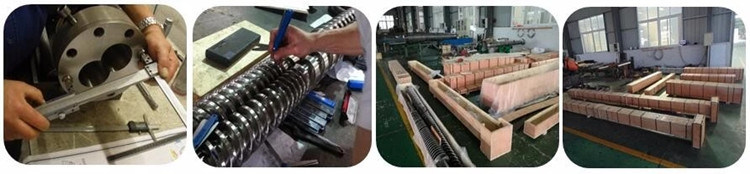
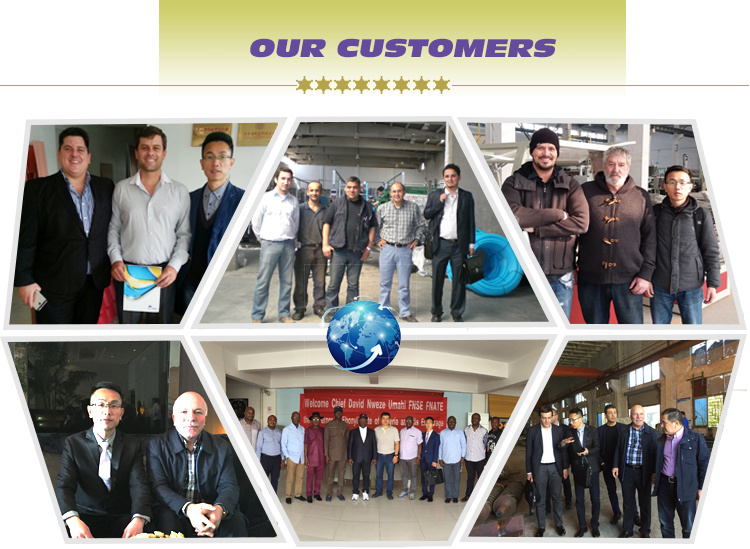
Please provide samples or requirements about dimensions and tolerances of , semi-finished and finished products, the equipment, the monthlly comsumption quantity, the current screw and barrel you are using, HRC and so on.
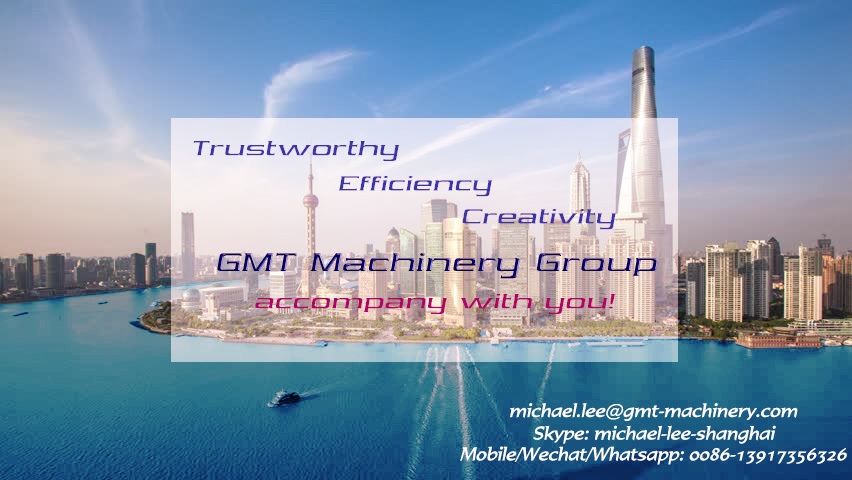
For more information, please kindly contact as below:
Mobile: 0086-13917356326
The main objectives of water treatment are:
1. Removal of suspended solids: This is usually done through processes like sedimentation and filtration to remove particles, dirt, and other suspended matter from the water.
2. Disinfection: Water treatment also involves disinfection to kill or inactivate harmful microorganisms such as bacteria, viruses, and parasites. Common disinfection methods include chlorination, ultraviolet (UV) radiation, and ozonation.
3. Removal of dissolved impurities: Many water sources contain dissolved impurities like minerals, salts, and organic compounds. These impurities can affect the taste, odor, and overall quality of water. Processes like ion exchange, reverse osmosis, and activated carbon filtration are used to remove these dissolved impurities.
4. pH adjustment: The pH level of water can impact its corrosiveness and taste. Water treatment may involve adjusting the pH level through the addition of chemicals to make it more suitable for its intended use.
5. Removal of specific contaminants: Water treatment can also target specific contaminants that may be present in the water, such as heavy metals, pesticides, and industrial pollutants. Advanced treatment technologies like adsorption, chemical precipitation, and membrane filtration are used for this purpose.
Overall, water treatment plays a crucial role in ensuring the safety and quality of water for drinking, industrial processes, agriculture, and environmental protection. It helps to prevent waterborne diseases, maintain public health, and conserve water resources.
RO Antiscalant Water Treatment, Silicon-Phosphorus Crystal for Water Treatment
Sichuan Jinhe Qihang Co,. Ltd. , https://www.jqfoodadditives.com